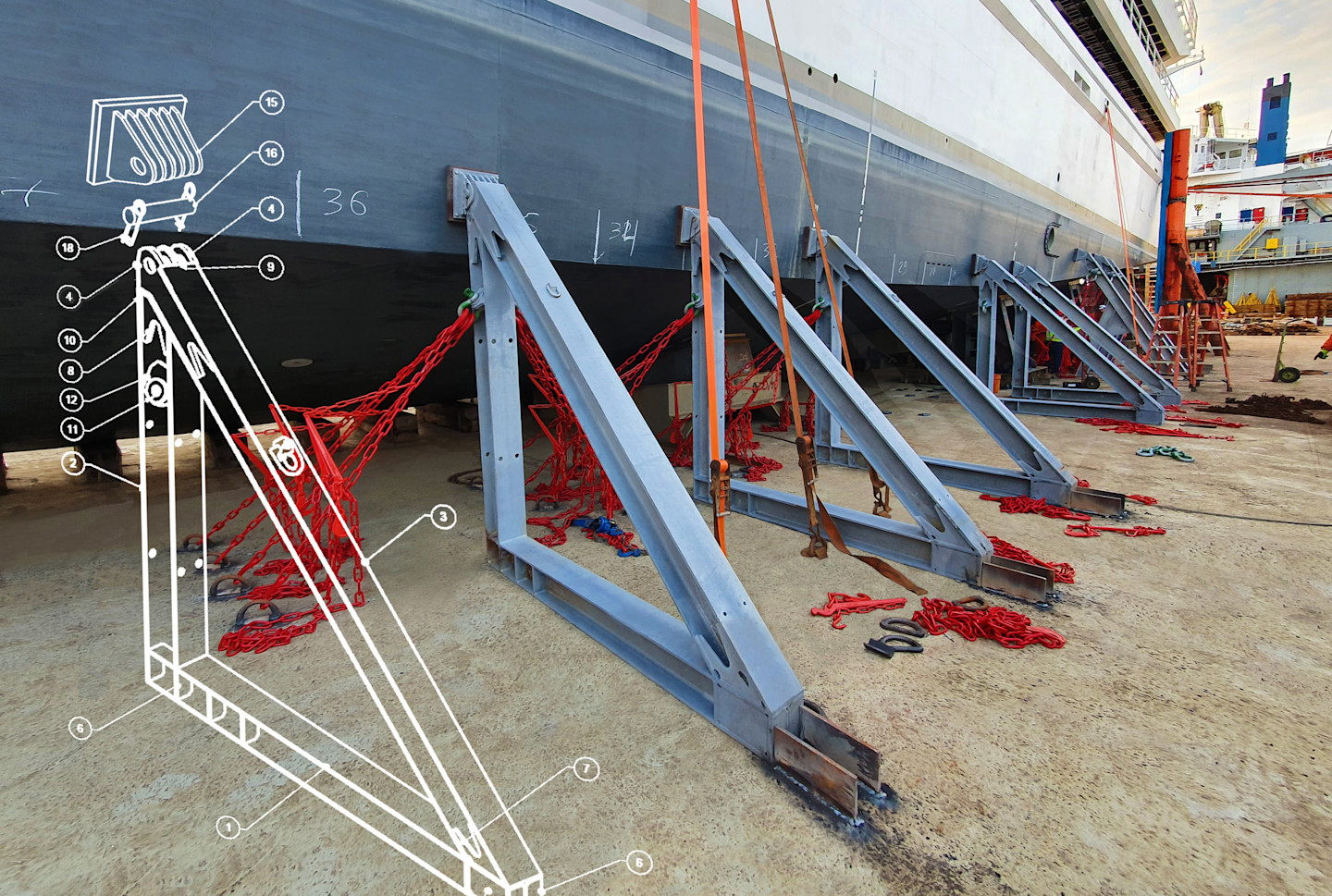
LET US CARRY YOU - LLOYD’S REGISTER ASSESSED SEA FASTENING EQUIPMENT
Two years of careful preparations, design, re-engineering, 3D modeling and calculations resulted in Lloyd’s Register Design Appraisals for most of Sevenstar Yacht Transport’s sea fastening systems. “Sevenstar is the first and only yacht transport company to have achieved this”, says Capt. Max Stepanov, Sevenstar’s Manager of Operations. As we talk to Max, also Sevenstar’s few remaining cradle designs are in the final stages of being reviewed by Lloyd’s Register. We discuss with Max and his team why they decided to take this route, what is involved in getting it done, how it influences daily work and what they believe is the technical route forward for the future of yacht shipping.
THE REASON: WHY “Sevenstar has come a long way since we started moving yachts back and forth in between Northern Europe and the Mediterranean in 1994”, says Jan Maarten Boissevain, the company’s sales director. “The days of the ‘Wild West’ in yacht shipping are certainly over and we have long since become a mature trade. Not only have our routes expanded, we also have significantly developed and improved our processes, procedures and stowage and lifting materials. The requirements have changed too: yachts that we load have become so much larger and yacht designs and building materials have changed significantly. Safety of our cargo, people and environment and establishing trust with our clients have always been at the heart of our operations.
With increasingly powerful modern tools engineering technologies available, it is both desirable and possible to keep improving on our quality. We are convinced that ‘rules of thumb’ no longer do the job and that investing in a more exact engineering approach with proof of compliance with international safety standards, is the way forward to stay ahead of the pack.” Capt. Max Stepanov, operational manager and one of the instigators behind the endeavour, agrees. “Thanks to our highly skilled in-house engineering team we were able to pull this off”, he says with a spark of pride in his voice. And rightfully so, the team worked on the project for two years, performed endless calculations and submitted hundreds of detailed drawings to Lloyd’s.
“We are constantly upping our game and so are our clients in the yacht industry” “Since the whole process is rather costly and a big investment to the company, we needed to build a solid business case before we could go ahead. There were no templates that we could just copy and adapt and getting an in-depth understanding of all applicable Lloyd’s Register rules was a major task by itself. The whole job required stamina from the team and a mindset of not giving up, despite the hundreds of calculation reports to produce and details to monitor. We are lucky to have such excellent engineering skills in house both at Sevenstar and at our sister companies Big Lift and Spliethoff. People with a rich background in marine engineering, naval architecture, cargo handling, 3D modeling, being at sea as Master and even working as surveyor for a class company contributed to the project. Next to the designs themselves, we wrote detailed instructions on how to deploy the systems in our Cargo Security Manual”.
Max adds that although improving safety was a key objective, getting the sea fastening designs re-engineered as part of the review process with Lloyd’s Register, also had significant other advantages for the company in terms efficiency improvement. For instance, they were able to design cradles and stands that are both lighter and stronger, and easier to handle on deck.
ABOUT LLOYD’S DESIGN APPRAISAL
Receiving Design Appraisal from Lloyd’s Register means that Lloyd’s has independently assessed our sea fastening designs for compliance with their rules and the purpose that the equipment is designed for. This includes design assumptions on how the systems can be deployed and at which loads”, explains Igor Parpura, engineer, and naval architect at Sevenstar. “In addition, Lloyd’s Register also witnessed and attested the fabrication of the sea fastening system models in question at an approved production facility. Confirming the Safe Working Load (SWL) is key: the capacity in metric tonnes for which equipment has been designed and built.
THE PROCESS: HOW The team started off with an inventory of existing cradles and stand models for both Sevenstar Yacht Transport and DYT Yacht Transport and researched areas to improve. At the same time an inventory and study of Lloyd’s Register rules applicable was done and a shortlist of sea fastening systems to be re-designed and submitted for assessment to Lloyd’s was created. For every single piece of equipment, usage and design assumptions, drawings and 3D models were created for a Finite Element Analysis (FEA). Engineers use FEA to simulate the behaviour of a part (or assembly of parts) under given conditions. The Finite Element Method subdivides a large system into smaller, simpler parts that are called finite elements, hence the name. The analysis (conducted through specialised software) uses mathematical models to simulate physical phenomena to understand and quantify the effects of real-world conditions on the design. The method is used to calculate for instance safe working loads (SWL), as well as to locate potential problems in a design.
Marian Minoiu, engineer and naval architect at Sevenstar, comments: “A major challenge was to incorporate the behaviour of cargo vessels into the equations of the FEA model for the various sea fastening designs. For instance, the rolling period of the vessel hugely impacts the acceleration forces on the yachts and thus on the cradling systems. Since cradling systems are used again and again, the calculation also needs to allow for fatigue.”
When all designs and models were in place, the information was submitted to Lloyd’s Register, who then assessed the designs again through independent calculations and analysis to confirm the assumptions behind the design and resulting in the final Design Appraisal. “This obviously, was a reiterative process with us going back to the drawing board several times”. “The design appraisal process has now been completed for the majority of our sea fastening systems and the last remaining cradle models are in the final stages of assessment at Lloyd’s”, says Max.
When asked about the main challenge during all of this, Igor Parpura answers that this was definitely ‘meeting the total of requirements while partially re-engineering the system’. “Not only Lloyd’s rules applicable for safety, but also our wish to design pieces of equipment that increase the efficiency of cradling. Equipment that is strong enough, yet lighter for easier handling on deck by the crew (and the divers on DYT’s semi-submersible vessels). Systems that are more versatile for use in many angles and positions, more efficient to lash down and that minimize welding time on deck. Other demands were more standardisation and less need for maintenance, for instance by applying top grade surface protection against the effects of sea water.”
WORKING WITH CRADLES Costa Thuring, who is both a Sevenstar loadmaster and also prepares cradling and lift plans for cargo operations, knows what it takes to work with sea fastening equipment. “A yacht is never the same” says Costa. “Even on production yachts the center of gravity may differ, depending on distribution of ballast like how much fluid is in the tanks, how many batteries and where they are stored.”
“Most clients appreciate this, but what they may not realise, is that when we prepare a cradling plan for a yacht, looking at the hull shape, strong points, dimensions, and weight of the specific yacht is an important but not sufficient part of the task. We also need to consider the detailed specifics of the actual vessel that will be carrying the yacht and calculate factors like what type of other cargo is on board, what is the vessels’ stability (and the expected rolling period), where will the yacht be placed on deck and in what way. All is required for to determining the best cradling plan and lashing setup for that particular yacht.
“The more accurate information we have on the yacht and the vessel, the more exact our rules and calculations for safe working loads and deploying cradling systems, and the better our cradles, the better we can prepare and the more quality we can deliver.”
Joost van Niekerk, Sevenstar’s logistics manager in Amsterdam, and Jan Moolman, Sevenstar loadmaster and the ware-house manager in West Palm Bach, both applaud the new approach and agree that for them the main requirements are: a) standardisation of equipment, b) reduction of maintenance work, and c) efficiency of transportation of the materials.
THE WAY FORWARD When asked about the future, Jan Maarten says: “With so many innovations happening in yacht building, our clients’ requirements are developing, and standards are being set at much higher levels. Our engineering approach is the way forward”. Max agrees: “We are ready to meet demands, this is only the beginning of an exciting process.”